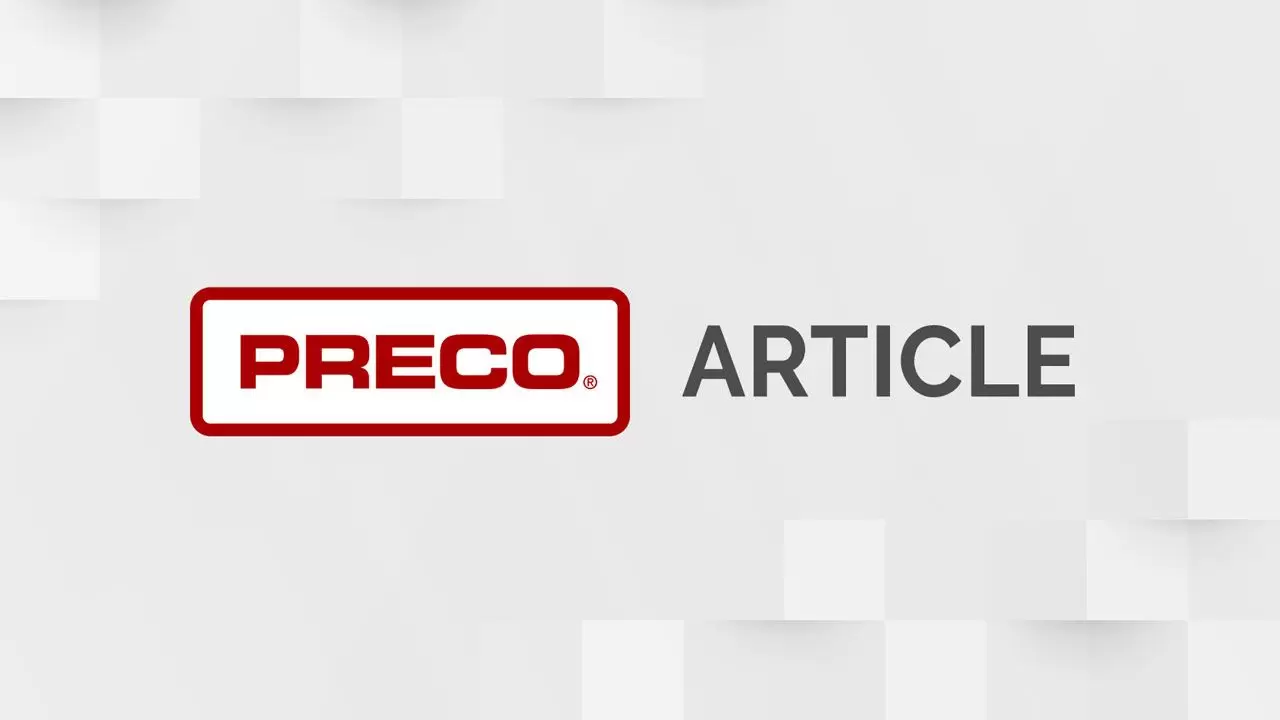
This article details recent advances in laser technology that are enabling gasket manufacturers to handle a wider variety of materials than before and to bid short run and intricate jobs that were previously uneconomical to quote. New types of lasers, laser delivery methods and laser platforms used to process a variety of non-metallic materials for the gasket industry are the focus of this article. In addition, operating costs, operator training, safety, and maintenance issues surrounding the use of lasers are included for consideration. Case studies feature how the introduction of lasers has dramatically changed the business of several manufacturers. Finally, the paper provides answers to questions frequently asked by manufacturers who are considering getting started with lasers – either by contracting with a laser job shop or purchasing a system for in-house production. |
Laser Basics for Die Cutting Fabricators
Laser System Development
Lasers began to make an appearance in industry in the 1970s for cutting and engraving. The 1980s brought the advent of laser cutting as part of CNC processes utilizing stepper controls. But what still limited the extensive use of lasers on many jobs was material processing expertise and quality control.
Along with the advancements in personal computer technology in the 1990s, the use of lasers in manufacturing became much more prevalent. The power of PCs enabled the integration of computer aided design (CAD) into laser systems. It became feasible to digitally design and implement a pattern through the same process.
A drawback at this time was that many systems had proprietary software and operating systems. However, most systems in the field today have standardized to the Microsoft Windows™ operating system, which allows for greater application flexibility and easier system upgrades and maintenance.
Another recent and significant development in lasers is system modularity. New "hybrid" laser modules can be added to rotary die cutting lines. These modular lasers are designed to work in a wide variety of production lines.
Adding laser technology to rotary die cutting greatly enhances speed by combining what had historically been two processes. Also, there is greater flexibility in the types of materials that can be processed with a hybrid system as both macro and micro cuts can be made.
The word, LASER is derived from Light Amplification by Stimulated Emission of Radiation. It’s an energy source, much like a light bulb. A laser works by transmitting a light beam – of one color in the spectrum – in a concentrated focused path.
A working laser was first demonstrated in 1960 at the Hughes Research Laboratory. It was originally thought of as a solution in search of a problem. Now, the greatest use of lasers is in optical storage devices such as compact disc and DVD players.
Laser System Development
Through the years, improvements in laser technology have produced steady increases in output power. Gases, dyes, crystals and chemical compounds are now used in common lasers to produce a variety of wavelength bands to meet different application and material processing needs.
Lasers are used in medicine for a variety of procedures including bloodless surgery, eye treatment, dentistry, and kidney stone reduction. Lasers are also found in a myriad of defense applications such as weapon guidance, target marking, and electro-optical countermeasures. Lasers are even used for packaging applications that require scoring for easy opening, or perforating for breathability.
New Developments In Laser Technology
New types of lasers
- Economical, low maintenance sealed lasers with up to 1000 watts of power.
- Higher powered UV lasers that produce better edge quality and the capability to produce finer cut features. This means cleaner and faster ablation (or removal) of certain materials.
- Alternative wavelengths that offer the ability to tailor the wavelength to a specific material type to improve cutting speeds and cut quality. For example, reduction of heat affected zones (HAZ), smoke accumulation, and charring.
Faster cutting without sacrificing accuracy
- High speed, high performance, motion systems that use fiber optics and faster, more accurate 2 or 3-axis galvanometers.
Integration options with material handling systems
- Modular lasers that can be added directly on to the die cutting process line. These lasers typically have a small footprint and can be adapted for use in prototyping all the way through full production. Many use galvanometer technology that allows process flexibility including kiss-cutting, perforating, scoring, slitting and through cutting.
What Lasers Do Well
While die cutting still remains a highly economical means to produce large runs using some materials, here are some laser advantages to consider when you are looking at your processes and system operations (See 1A)
One of the main advantages of lasers is the flexibility it gives companies in taking on a variety of jobs – especially small or specialty work. Lasers eliminate the need for tool and die fabrication, as well as the need to maintain and store dies. Laser control systems use digital CAD files to aid in just-in-time manufacturing. Repeat orders can be retrieved and duplicated in minutes.
Basic Types of Lasers Used with Non-metallic Materials
Today, most Fiber and Nd:YAG type lasers are used in metals processing operations. Typically, ultra violet (UV) and Fiber lasers use diode pumped solid state (DPSS) technology. New lasers are being developed that use alternative wavelengths that will expand the capabilities of laser processing.
Lasers used in the non-metal gasket industry can generally be divided by the wavelength required. Most use CO2 gas or ultraviolet wavelengths to process materials such as polypropylene, polyesters, and polyimides.
Laser Delivery
Depending upon the material and product used in the process, a laser beam delivery option needs to be made. Delivery of the laser beam is typically accomplished in one of the following ways:
- Fixed Beam – XY table moves the material
- Flying Optic – XY moves beam over stationary platform
- Galvanometer – Steered or directed beam with or without any material motion.
- Robotic Motion
Laser Platforms
What are galvos, XY systems, XY tables, and flying optics? These are all types of laser platforms designed to handle different types of materials. Lasers and optics are continuously improving providing the capability to process faster, cleaner and more accurate cuts.
Some platforms are designed to primary handle sheet stock materials, some web stock materials, and some both. Further, laser beam options impact the spot size on cutting speeds and power requirements. The following is a simple comparison of platform types and performance:
Platform | Position Accuracy | Relative Cost |
---|---|---|
Stepper | Low | Low |
Belt Drive | Low | Low |
Rack and Pinion | Medium | Medium |
Ball Screw | High | High |
Servo (Rotary) | High | High |
Servo (Linear Motors) | High | High |
Important Issues for Achieving a Quality Laser Cut
HAZ – Heat Affected Zone is typically considered undesirable because this condition can leave burrs, a ridge or even discoloration on the material. There are times however, with adhesives for example, that it can be an advantage as HAZ will cauterize the edge and not allow the adhesive to flow, thus providing better edge quality.
Kerf Width & Taper - Kerf is the amount of material the laser removes. Taper is the difference between the kerf at the top of the cut and the bottom of the cut. Ideally, most materials are processed so that the kerf is equal all the way through the material. This set up can be achieved by setting the focal point correctly.
Focal Length - A lens is used to focus the laser beam to a spot. A short focal length creates a tight spot with higher power density.
Assist Gases – Typically, when cutting nonmetals, assist gasses are not used. However, the two most commonly used gasses are compressed air and nitrogen.
Spot Size, Power Density & Impact on Cutting Speed – A fast cut requires the use of a tight spot with high power density. Another consideration is desired edge quality. For example, acrylic can be cut fast, but in order to create a fire polished edge it must be cut at a slower speed.
Special Lenses (Telecentric Lenses) - Telecentric lenses are used to help correct the angle of the beam in the entire field of view. These lenses orient the beam perpendicular to material when galvonometers are used in the process. Telecentric lenses are beneficial in minimizing taper and when cutting geometry is close to the edge of the field of view. However, telecentric lenses can only be used for small cutting areas.
Thermal Distortion – Thermal distortion is an undesirable situation where heat causes material to ripple or warp. It is similar to the condition found with HAZ.
|
Stop/Start Marks - Stop and start marks result from the point where a laser enters the material to where the cutting process ends. If the geometry of the cut is such that the line comes back to meet the initial start mark, there may be some overlap. This condition may be more evident on some types of materials.
Other issues to consider for control of cut quality include:
- Accuracy
- Taper/angle
- Power level
- Productivity rate
- Edge quality
- Distortion
Advantages of Using Lasers in the Gasket Industry
The use of lasers has other advantages over die cutting in processing because there are no die setup costs, no die maintenance, and no storage costs. If a project is recalled into production, a digital program can quickly be retrieved.
Materials Flexibility - Abrasive, adhesive, cork, paper, rubber, silicone, steel, and many types of polymer materials are all prime candidates for processing using laser technology. Laser cutting produces exceptional edge quality, important when processing these materials. Also, laser cutting leaves little or no burrs, debris, or strands on the material edges. Further, applications are not limited to just cutting — welding, heat treating, and marking are also common uses for laser technology.
The table below provides information about laser cutting of various materials typically found in the gasket industry. However, the linear speed listed is based on a single system and is not intended to indicate optimal parameters for any specific material.
Flexibility in the Types of Jobs - When a job requires a quick setup or a pattern change, the use of lasers cannot be beat. Similarly, if the project requires a great deal of vision alignment and registration, laser technology allows the operator to register parts before processing and align the cut pattern registration features – either printed or mold features.
Reduced Time to Proficiency for Operators - With the wide acceptance of Microsoft Windows™ computer operating systems, the training of laser systems operators has been greatly simplified in the past several years. The typical steps in training a laser operator are simply to:
- Generate a program file (CAD or CNC)
- Create a laser parameter and recipe storage file
- Execute the program file
Once an operator has mastered these fundamental steps, new jobs can be rapidly set up on the laser system.
Laser Safety and Maintenance - There are some safety and maintenance issues that must be taken into account when using a laser. First, safety issues include awareness that when working some materials like PVC, noxious gases are emitted during the cutting process. Common solutions to safety and quality issues include the installation of air flow handling equipment and masking devices.
For the most part, the newest generation of lasers are sealed systems that require little maintenance. Typical failure points in a laser system are usually the external optics, especially when they are not properly maintained. To prevent laser optic failure, routine maintenance includes periodic cleaning.
A Real Life Job – Done with Lasers
As an example of how lasers expanded the versatility and profitability of one company, a Canadian medical device manufacturer recently enlisted the help of a laser contract firm to complete a job creating polyester gaskets with adhesive backing. The application required making a small cut feature in the gasket lamination.
The existing manufacturing process used by the company allowed adhesive to flow back into the cut opening, creating unacceptable parts. The laser system used by the contract firm proved to be the only reliable method of processing by providing a cut that both vaporized and sealed the edge. The laser process eliminated the adhesive reflow.
With this success, the company retained the laser contractor to do short production runs. Eventually, the product required production runs up to 100,000 parts per month. The company then found it to be economical to purchase a laser system of their own. Overall, using the laser process enabled the company to get a precision, high quality part quickly and reliably to market.
How to Get Started with Lasers
If your company has been strictly a die cutting operation, you don’t necessarily need to “no quote” jobs that require laser cutting. Here are a few steps to get you started:
Pick a Knowledgeable, Established Supplier - There are many companies that specialize in laser cutting to whom you can sub-contract to enhance your capabilities. As in hiring any subcontractor, it is important to do a little research on the laser job shop’s performance history and equipment capabilities. Places to start looking for a reliable, experienced laser contractor in your area include:
- Industry networking
- Internet searches
- Trade shows
- Trade journals
Here are some questions that can be asked of a prospective laser contractor:
- What platforms are available? Check that they satisfy your manufacturing requirements. For example, can the platform handle flat sheet or roll stock?
- What tolerances can be held?
- Are samples of cut quality and speed for specific materials available?
- What types of digital file formats can be accommodated? For example, which CAD and CNC file types are accepted?
Again, a little research will go a long way. It is important to ask a potential laser contractor about their expertise and equipment in applications similar to your business. Checking a prospective laser job shop’s references about service and response times is also important.
Cost Considerations - At a certain point, the amount of jobs that you choose to bid may reach a volume that will justify the purchase of your own laser system. There are a wide range of costs for laser systems depending upon the complexity of the job needs:
System Type | Cost Range | Applications |
---|---|---|
Lower Power Systems | $30,000 to $50,000 | Sample Production |
Standard Commercial Power | $100,000 to $350,000 | Non-Metallic Job Production |
Special Commercial Systems | $400,000+ | Variety of Applications |
How to Find or Train Laser Technicians – In many cases, the best place to find a good laser technician is from within your existing group of die cutting operators. Senior employees already have a good sense of overall shop floor practices and typically can be trained to work with the digital files required to process materials with a laser.
However, if you choose to hire a dedicated technician a good starting point would be schools offering laser/electro-optics programs, such as Texas State Technical College Waco, Indian Hills Community College, or Idaho State University, to name a few. Other suitable technical backgrounds to consider are machining and programming.
Laser Resources – A great reference guide about lasers is the Laser Institute of America Guide to Laser Cutting. This book is available through the Laser Institute’s website, laserinstitute.org or by calling 1-800-345-2737. Several periodic journals can also be recommended:
How Much Does It Cost to Run a Laser System?
The laser system uses a variety of support systems based on the type of material being cut. In a typical application not all of the sub-systems are used simultaneously but are presented here for a "worst" case scenario. The example is for a 200 – 400 watt sealed laser, but does not include overhead or depreciation of the system.Main system: Laser System
- 208 Volt, 3 phase, 45 Amp, consumes ~9KW/Hr. Therefore, electrical for main system is ~$0.60 per hour based on a $0.065 KW cost
- Compressed Air (if required): 10 CFH at $0.003/CF. Therefore, compressed air is ~$0.030/Hr cost
- Vacuum Blower (if required): 3 HP blower at ~2KW/Hr. Therefore, vacuum blower cost is ~$0.135 per hour based on a $0.065 KW cost
- Chiller: 208 Volt, 3 phase, 30 Amp consumes ~6KW/Hr. Therefore, electrical for chiller is ~ $0.40 per hour based on a $0.065 KW cost
- Nitrogen (occasionally required): 10 CFH at $0.0072/CF. Therefore, Nitrogen cost is ~ $0.072 per hour
- Production Labor at $ 16.00 per hour
- Main System: $0.60 per hour
- Support systems: $0.637 per hour
- Production Labor: $16.00 per hour
- Grand Total: $17.237 per hour
Growing A Laser Processing Business
One of the nations largest laser job shops, also happens to be one of the oldest of its kind, dating back to 1978. The business model was quite unique, and remains in tact to this day. Leveraging CNC machine design skills, the company positioned itself to provide both laser contract manufacturing services, using flexible laser work stations built and maintained in house, and/or provide turnkey industrial laser equipment to be installed at a customer’s site.
The initial primary focus of the companies’ contract manufacturing was in the area of laser engraving of wood and plastics. What started as a three person company operating a single CO2 laser in the basement of the owner’s house, transitioned to several lasers in a pole shed cutting a variety of metal and non-metal components.
Today, the company has expanded in several key ways. Now more than 40 laser work stations process a variety of materials for the metals and converting markets. These lasers work stations vary in both power and wavelength to match specific processing needs. The company has also invested heavily in an applications development staff through the years to perform research and development to provide a continuous stream of leading edge laser technology to be used in new contract work, or the continued sale of laser equipment.
An additional strategy the company has utilized is to pursue a diverse mix of both laser applications and markets. Current markets include alternative energy, electronic thin film, packaging, medical, aerospace, automotive, precision industrial gaskets, heavy off road, and more. Technical, quality, and production staff are strategically organized by target market, and the overall business mix allows the company to hedge against industrial or economic downturns, and remain healthy and stable.
Why Not Use a Laser to Get the Job Done?
The use of lasers can greatly add to the types of jobs that a gasket manufacturer can tackle. While die cutting may still be the most economical means to produce certain products, laser technology now provides manufacturers with tremendous process flexibility and the ability to work with more materials. Further, lasers are an economical means to complete intricate, high quality jobs.